Visionaize V-Plant Powers Digital Twin Transformation at Mitsubishi Gas Chemical
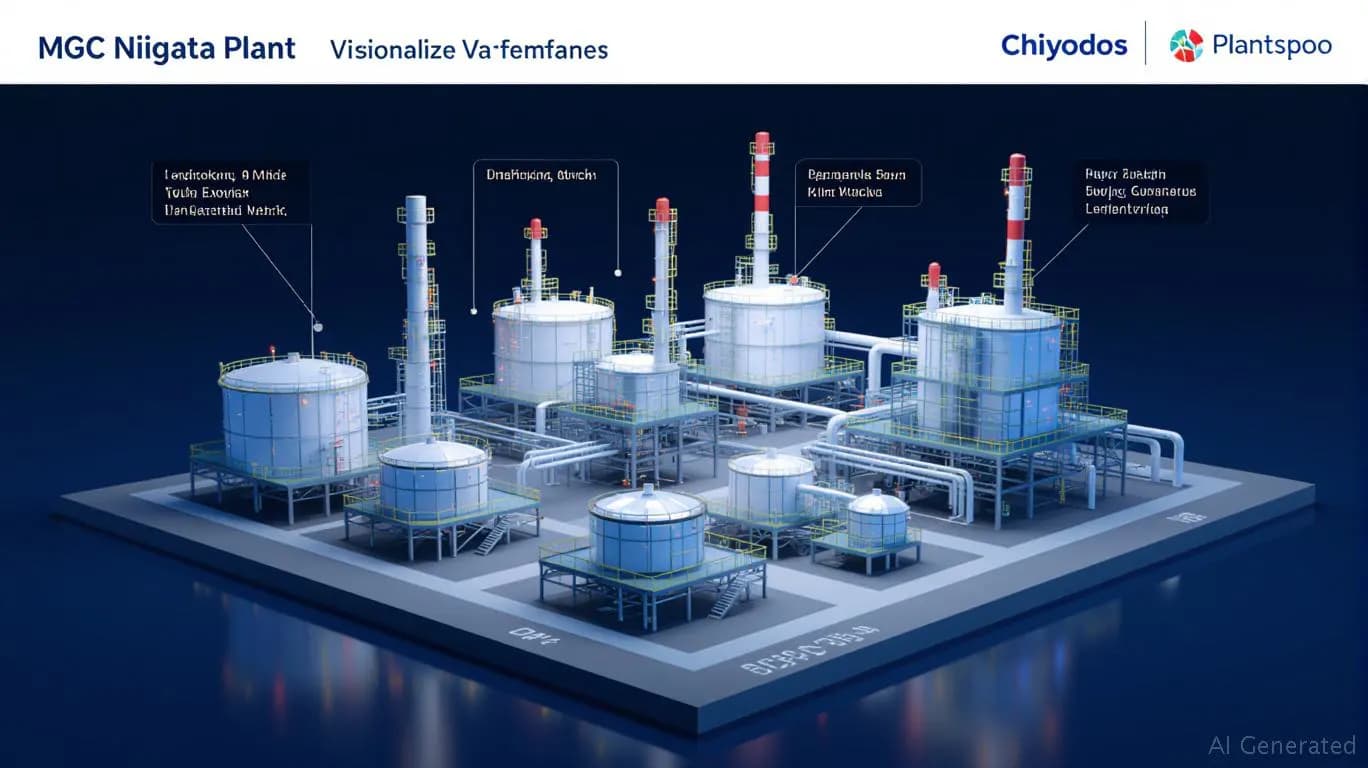
Japan's Chemical Giant Embraces Immersive 3D Visualization for Smarter Operations
The industrial sector is undergoing a rapid digital transformation, and Japan's Mitsubishi Gas Chemical (MGC) is leading the charge. Visionaize Inc.'s V-Plant platform has been selected as the core 3D Digital Twin visualization engine within Chiyoda Corporation's plantOS framework at MGC's Niigata Plant, marking a significant advancement in the country's chemical manufacturing capabilities. This partnership promises to unify data, enhance safety, and unlock operational intelligence through immersive 3D environments.
Key Points:
- V-Plant Integration: Visionaize’s V-Plant platform will serve as the visual and contextual data engine within Chiyoda's plantOS, providing immersive 3D visualization.
- Phased Implementation: MGC will adopt a tiered approach, starting with panoramic image integration and progressing to a comprehensive, navigable 3D Digital Twin.
- Strategic Partnership: The collaboration combines Visionaize's 3D visualization expertise with Chiyoda's deep domain knowledge in plant operations.
- Unified Data & Intelligence: V-Plant contextualizes data, connecting documents, assets, and operational logs within a unified 3D experience.
- Tiered Digital Twin Maturity: The phased rollout includes Panoramic Image Integration, Mesh Model Visualization, and ultimately, a Full Digital Twin.
The selection of V-Plant isn't just about pretty visuals; it's a strategic move towards a more data-driven and efficient operation. Traditional plant management often involves siloed data sources and disparate systems, hindering real-time decision-making and potentially impacting safety. By integrating V-Plant, MGC aims to break down these silos, providing a single, unified view of the entire plant. This immersive 3D environment allows engineers and operators to virtually navigate the facility, access critical information, and collaborate more effectively – all contributing to improved productivity and reduced risk. The phased approach, starting with simpler visualizations and progressing to a full digital twin, demonstrates a pragmatic strategy, ensuring a rapid return on investment while allowing MGC to gradually build its digital maturity.
The adoption of mesh models as an intermediate step between panoramic images and full digital twins is particularly noteworthy. Mesh models offer a significant upgrade in realism and functionality without the complexity and cost of a full CAD-grade model. This allows for broader use cases like hazard mapping and remote collaboration, expanding the platform’s immediate value. This also allows for a more controlled transition to a fully realized Digital Twin, ensuring that the technology aligns with evolving operational needs and priorities. The move underscores a growing recognition of the power of 3D visualization in industrial settings, particularly in Asia.
The partnership between Visionaize and Chiyoda highlights a broader trend in the industrial sector: the convergence of specialized technology providers and established engineering firms. Visionaize brings the cutting-edge visualization technology, while Chiyoda provides the deep operational expertise and system integration capabilities. This synergistic relationship positions both companies for continued growth and innovation. Looking ahead, we can expect to see further adoption of similar digital twin solutions across the chemical and other industrial sectors, driven by the need for greater efficiency, safety, and sustainability.